Stop Tribocharging Your Products
- Published: May 01, 2009, By By Dr. Kelly Robinson Contributing Editor
The cheapest and most reliable way to solve a static problem is to stop it before it starts. Prevention is the best cure. Most static problems start with tribocharging between two different materials that touch and separate.
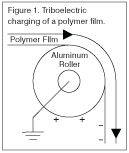
Think about an insulating polymer film running through a converting process (see Figure 1). The film touches many conveyance rollers as it moves through the process, and the film is different from the rollers. With each roller contact, the film gains some charge, and the roller gains an equal amount of opposite charge. If the roller is conductive, its charge flows through the bearings to ground. When the film gains too much charge, static problems happen, like dust attraction, sticking, blocking, and sparks that can damage the film surface or disrupt the machine control system.
So, what can you do to reduce tribocharging? If you are running the process, the first things to do are to clean the rollers and reduce the film tension. Many static problems are caused by dirty rollers or film tensions that have crept up and now are higher than normal.
If you are a machine designer, choose rollers with some surface roughness to reduce the contact area with the film, which reduces tribocharging. For example, the surface texture of a hard coated aluminum roller reduces tribocharging.
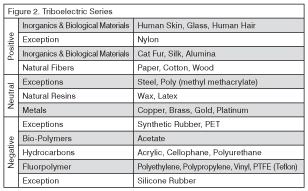
Also, choose roller materials that are compatible with your customer's products. To choose compatible materials, use the Triboelectric Series as a guide (see Figure 2). A material that is higher on this chart will have positive charge after it touches a material that is lower. For example, a polypropylene film will have negative charge after touching an aluminum roller. The surface of aluminum has a thin layer of aluminum oxide or alumina. While this layer may be only one or two molecules thick, this is thick enough to determine tribocharging properties.
Materials that are closer together are more compatible. For most polymers, hard coated aluminum or steel rollers are good choices. For covered rollers such as drive rollers or nip rollers, polyurethane is a better choice than silicone rubber.
The materials in the Triboelectric Series fall into groups such as “natural fibers” or “hydrocarbons.” Use these groups to estimate the position of a material that is not listed. Be aware that there are exceptions. For example, nylon is unusually positive compared with other polymers. Similarly, silicone rubber is unusually negative.
If you are a product designer, know that coatings and printed surfaces of your product will determine its charging properties. You can solve many static problems before they start by formulating the surfaces of your product for good static performance in the converting process. buy dnp
Get rid of the static at the source by selecting compatible materials and by keeping surfaces clean. Prevention is a cheap and reliable way to solve static problems.
Static control expert Dr. Kelly Robinson, president of Electrostatic Answers, has 27+ years of experience in problem-solving and consulting. Contact him at 585-425-8158; This email address is being protected from spambots. You need JavaScript enabled to view it.; www.electrostaticanswers.com.