Gravure Versus Flexo Printing Part 2
- Published: August 01, 2009, By By David Argent Contributing Editor
Last month I outlined the rapid growth of flexo printing in packaging and suggested that gravure printing had been out-marketed in North America by a very determined flexo community, which continues to gain share. Gravure printing today has many technical advantages for the packaging market that sometimes are overlooked. In addition there have been enough gravure improvements to warrant a reassessment of some of the old paradigms of cost, setup time, and run length.
Technical Aspects of Gravure
This is a very simple process with only a single impression to be set, so there are few inherent variables making for high quality print within the run and from run to run. Line and process can be combined on a single deck with the possibility of running fewer total color stations on the job. It is possible to carry very heavy ink films in gravure and maintain print resolution. With a commonly used solid cylinder, about 9 wet lb/ream can be delivered. This is about three times the flexo rate. If you compare the two ink delivery systems, there are two ink film splits in flexo and only one in gravure. The advantage of this is that gravure is capable of producing unmatched white ink opacity, vivid metallics and fluorescents, and many other specialty effects and functional coatings not achievable in flexo. The gravure inking station allows use of very strong solvent mixtures that often are high in acetate content, which, in turn, allows for more possibilities in ink formulations. The high line resolution of gravure is a plus for small packages when ingredient labeling type is challenging for flexo.
Manufacturing Aspects of Gravure
Many times comparisons are made between state-of-the-art flexo presses and old clunker gravure equipment. The current situation is that new flexo and gravure presses are about equivalent for features, amenities, and also for cost. All of the advanced robotic controls and features for flexo are available for gravure, so the playing field is now level. This requires that the traditional chart for gravure break-even analysis (see figure) be revisited. Opinions are numerous, but data is rare.
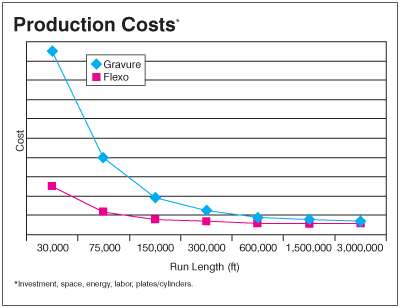
One analysis1 available online makes a good case for gravure economics and is backed with data. The essence of the argument goes like this: The prepress cost of gravure should be spread over repeat runs when the durability of the cylinder comes into effect and run length is less relevant. The cost of producing gravure cylinders is not proportional to the design complexity but is fixed and based on unit area of engraving. With flexo, the cost of plates increases with complexity of design.
Manufacturing improvements continue for gravure and include laser engraving of cylinders. Lightweight sleeves are available now and allow for easy handling, storage, and shipping.
Marketing of Gravure
The Gravure Assn. of America and Packaging & Label Gravure Assn. Global are good forums for initiatives to promote gravure printing in packaging. If the history of flexo packaging growth is an example, it will take initiative and dedication from the supplier community to clearly define and optimize the steps in the total gravure workflow and communicate this process with print buyers.
There are indications that gravure as a process is beginning to take this initiative. We should see some interesting developments and an increased level of competition as these two processes battle over their share of the market.
1http://www.chesnuteng.com/gravure_casestudy.html
Process improvement expert David Argent has 30+ years of experience in process analysis with particular emphasis on ink and coating design and performance. Contact him at 314-409-4304; This email address is being protected from spambots. You need JavaScript enabled to view it..