On Print | Value Proposition for Thermal Transfer: Printed Electronics
- Published: March 09, 2017, By Dene Taylor
Thermal transfer offers a unique set of capabilities that can be applied to advantage in emerging applications, one of which is printed electronics.
The Digital Printing Value Proposition states the common keys for digital printing in the graphics arts and packaging markets (Table I). They are the differentiators from analog technologies that many customers need to satisfy the demands they face. But to provide these values, the printer has to have reliable, cost-effective production capability. As an example, for folding cartons there are now excellent presses using liquid or dry toner and aqueous or UV cure inkjet, at prices with attractive ROI.
But not all markets or market sectors where the Value Proposition can apply have been penetrated. For example, absolute cost for first entrant has stalled inkjet printing of flexible packaging to match a central impression (CI) press. The components are available, but the first complete implementation has a very high cost.
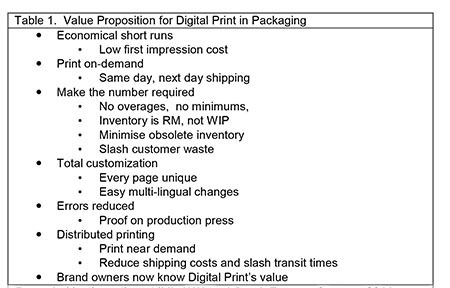
The printed electronics business is now experiencing the same values. By far the bulk of the conducting elements in circuits are formed from metal foil laminates that are masked by analog printing and then etched. Matching the conductivity by analog printing metallic ink has an increasing role, but the inks are costly and must be sintered, a process more costly than printing. Inkjet has some penetration, but it suffers also because of the cost of the materials, the cost of the equipment, and the complications of the fluid. And without a digital conductor, there is not much demand for other layers to also be digital.

An example is the production of the antennas for RFID tags operating in the UHF band (see Figure 1 and Figure 2), which have mid-range conductivity needs. Billions of a just few designs are produced by etching and so have very low cost. But that makes the supply chain similar to that for flexible packaging—large minimums, long lead times, high initial cost for even minor changes, and so on.
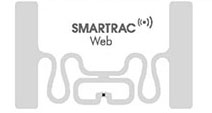
There are smaller analog processes but they too are complicated—getting highly conductive metal is the problem. IIMAK, the thermal transfer ribbon manufacturer from Amherst, NY, recognized the void and developed conductive aluminum and copper, plus dielectric ribbons to fill this void.
Thermal transfer printers are ubiquitous – every facility shipping liquids has at least one for container or shipment labeling. They are reliable, robust, rarely have ink (ribbon) problems, and are simple to use. So let us look at Thermal Transfer Printing’s Value Proposition:
Economical short run
Analog compared to digital has high changeover and start-up costs. With immediate cold start printing, changeover effort and time is now dependent on chip attachment, which is digitally controlled so can be quick, and die-cutting, which with laser is also immediate. Waste need be only a few repeats taken to ensure the change was correct.
Print-on-demand and make the number ordered
Thermal transfer does this for label printing—a finished print emerges only a second or two after (print) is pressed, and the number is exactly as requested. These are the keys to reducing inventory, eliminating WIP (work in process), and minimizing obsolescence, all these costs should be added to the product pro-forma costing.
Productivity is essential if digital is to provide the above values—the minimum speed for thermal transfer is 2 ips (50 mm/sec), with high quality achievable at 6 times that (60 fpm or 18 m/min). This compares with the other methods, and matches the rates for in-line tag assembly.
Errors reduced
The antenna design engineer can have a thermal transfer printer at the work station, running the same ribbons and substrates. The file for production can be the same as used for qualification of the prototype, so no special scale up activity. Quality assured before the press also reduces errors and waste. The ribbon producer handles the trickiest component—the fluid phase of the ink—and has high levels of inspection. The printer has no ink viscosity issues, no settling, no gelling, no rollers fouled, and no drying or curing, and no odors, ozone, or VOC (volatile organic compounds).
Operator familiarity with thermal transfer for RFID tag production is high—it is the dominant technique for printing logos, part numbers, and serial numbers on tags, simultaneously with programming the chip.
Capital costs
Monochrome printers with internal rewinders are not merely bench-top printers, they can be stand-alone production cells with costs of just a few thousand dollars. They also can be the master drive for a tag production cell, using the add-on for a die-cutter. The multicolor printers offer multilayer printing in tight registration and close proximity, which can be useful for antennas, especially for printing coils, which need insulated bridges.
Distributed printing
Compared to wet production methods (etching, screen, and inkjet) thermal transfer is simple, clean, highly productive, known, and has low installed cost. It has negligible direct impact on ROI calculations. None of the alternatives come close on any of those measures. They are not simple well-known devices, their processing is not instantaneous, they are not instant on/off, and need to be cleaned up before being shut down. They have much larger footprints, and they are 10 to 20 times more costly to buy and operate.
Electronics opportunities for production by thermal transfer are limited by the metal thickness being sub-micron—thicker layers do not fracture cleanly. Over printing with multicolor printers extends the range but not to the conductivity required for current NFC RFID, for example. On the other hand, there are multiple incentives for low current technologies, which obviously expands applications. Dielectric ribbons are easier to make and market requirements for variants will be met.
The Value Proposition also applies to printed electronic research and development institutes, especially those attached to universities. Thermal transfer offers new capability—developers and designers can make things they couldn’t make before, faster and at less cost. And they can produce one or one hundred thousand without trying to learn how to scale up in a separate pilot facility. And those investigating inks can make experimental ribbons by draw down suitable for proof of concept. Basic lab coaters can be used for prototypes. Materials of interest include graphene, carbon nanotubes, silver, and other metals.
Right now we are focused on developing opportunities in printed electronics and will be pleased to hear from anyone with an interest in that area (check out our website). More importantly some of you will recognize quite different opportunities where the novelty or the Digital Print Value Proposition applies, and I encourage you to look into them. Additionally there have been useful discussions at the IMI Thermal Printing Conferences chaired by Al Keene and Harry Schofield that may help you identify others to contact.
Printing expert Dene Taylor, PhD, founded Specialty Papers & Films Inc. (SPF-Inc.), New Hope, PA, in 2000 for clients seeking consultation for technical management, new product design, development, commercialization, and distribution, as well as locating/managing outsourced manufacturing. Contact him at 215-862-9434; This email address is being protected from spambots. You need JavaScript enabled to view it.; www.spf-inc.com.