Westpak Chooses Comexi Laminator with Vetaphone Corona
- Published: September 30, 2019
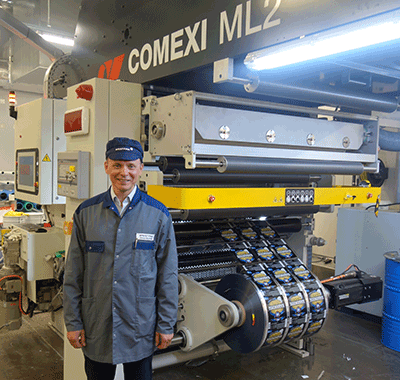
Westpak Oy AB has installed a Comexi ML2 laminator at its production facility in Säkylä, some 200km north-west of the capital city of Helsinki. Significantly, it is one of the first of the new Comexi laminators to be fitted with Vetaphone Corona technology under an agreement between the two companies at the launch of the ML2 series in 2016.
Westpak, which was established in 2008, brings a wealth of experience and expertise to the short-run printed packaging markets of Scandinavia and the Nordic countries, and chose the Comexi ML2 with this requirement in mind. Speaking for the company, Managing Director and co-owner Jonas Skuthälla explained: “We needed a machine that was quick and easy to make-ready to facilitate the frequent job changes necessary to supply our local markets. The Comexi offered the flexibility we needed to use different adhesives, was a proven design, and offered us a degree of future-proofing as demands change in the industry.”
The ML2 is a top of the range machine designed for both high productivity and versatility and is intended to build on the success of Comexi’s popular Dual model, which it replaces. It is a true ‘operators’ machine’ with a range of gadgets that make it easy to operate, and fast to run. Capable of running solvent, water-based, or solvent free adhesives, the ML2 has a maximum web width of 1530 mm and is capable of 450 m/min, offering cold seal, heat seal, ink, matt and gloss varnish, as well as all kinds of in register applications. Its trolley design permits gravure, solvent-less, flexo, semi-flexo and enclosed doctor blade chamber operation, and customers can specify drying tunnels up to 9 metres long, with independently controlled sections.
The decision by Comexi to recommend Vetaphone equipment on the ML2 was taken after extensive tests of the Danish technology and is hailed as a mark of best practice for Vetaphone. The system chosen for Comexi is the newly developed VE1L model that is capable of treating conductive and non-conductive materials and is supplied with the high-efficiency iCorona generator that Vetaphone describes as “state-of-the-art.”
Commenting on the new working partnership that has been forged between the two manufacturers, Vetaphone’s VP of Sales, Kevin McKell said: “We are delighted to be working so closely with such a leading wide web manufacturer as Comexi, whose technology is universally respected and admired. For our Corona technology to be approved and recommended for the new Comexi ML2 is key milestone for Vetaphone as we aim to extend our market penetration in wide web.”
Responding for Comexi, Brand Manager Carles Rodríguez confirms that collaboration with Vetaphone was excellent right from the beginning: “We have very strict and demanding specifications that have been successfully achieved during our comprehensive tests. We are more than pleased to welcome on board such a talented group of professionals, with the latest state of the art technology products.”
For Westpak, the tie-up could not have come at a better time, according to Jonas Skuthälla: “The combination of Comexi and Vetaphone is ideal for our operation here. Both are highly respected brands within their own sectors and offer the reliable performance that is essential when you are running 24/7 in a competitive marketplace. We especially appreciate the family business ethics of both companies which translates into excellent after sales support and service,” he said, adding that the new laminating line had performed well and met all expectations since being commissioned. Fitted with a camera to offer lacquering in register, it has allowed Westpak to move some of its cold seal production off the press, and free-up capacity for more print.
The company reportedly prides itself on its efficiency and high-quality work. Operating a policy of transparency with its customers, the management is very hands-on and the production process as lean as possible. According to Skuthälla, the company has a programme of continual investment in the new technology that it believes is essential to compete effectively. Beginning with a simple package of equipment that included a flexo press, laminator and slitter/rewinder, the company soon saw the need to refine its capability with the high-quality technology. “When we test new equipment prior to placing an order we always take our operators with us – they have the day-to-day responsibility of making it work profitably. It’s judging the balance between price and performance that’s important and we believe in empowering our people by giving them responsibility.”
For more information, visit www.vetaphone.com.