Robinette Company Improves Production Efficiency with Martin Automatic Technology
- Published: February 25, 2019
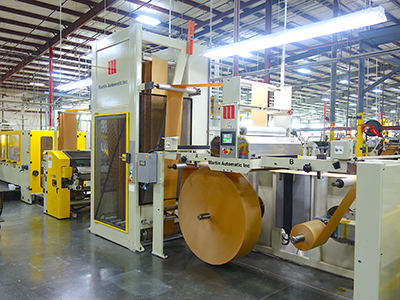
The Robinette Company has a history dating back to 1938 when it was supplying paper bags to the flour and corn millers of the eastern USA. Today, the company is a full-service flexible film and paper packaging manufacturer and converter specialising in sustainable packing for the food, beverage, nutraceutical, construction, textile and health care markets
Operating 20 machines the Piney Flats plant produces more than one million quality bags per day, and Robinette is now reportedly the largest supplier of charcoal bags in North America. The Piney Flats facility is capable of manufacturing a variety of SOS (Self Opening Square), pinch bottom and can lid bags on its 12 Weber, four Matador and two new Holweg Weber lines.
The performance capability of the new Holweg RS 37 lines warranted automated roll changing, and the company turned to Martin Automatic to specify and supply the technology, based on its experience with the manufacturer’s equipment on a narrow web press at its Bristol facility. The result is an installation of two of the manufacturers MBS non-stop unwind/butt splicers that are mirror images of each other to allow one operator to handle both splicers with ease.
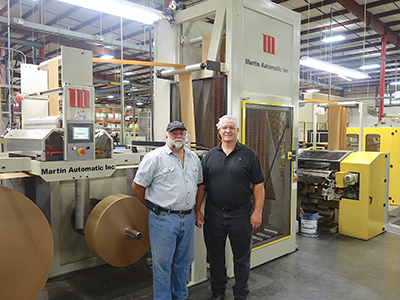
The two Holweg lines are capable of 400 bags/minute on a web width of 900mm. They are designed for long bags (up to 1500mm) using paper stocks from 70 to 125gsm. Cut-off is variable from 400mm to 1560mm depending on the number of grippers, and bag widths can be from 70mm to 380mm, with up to 80mm gussets. Standard flap size is 40.3mm. The Martin MBS unit on each machine changes rolls automatically, without slowing or stopping the line. Importantly, each Martin is equipped with a “spot-splicing” feature and integrated with the Holweg so that splices avoid the perforating knife and tucking blade, preventing machine damage and downtime.
“The two Holweg/Martin lines have produced as many bags in the first eight months of 2018 as the five decommissioned Matadors managed in the whole of 2017,” said Tim Wilhoit, plant manager at Piney Flats. “We have also seen a reduction in staffing levels of 29 percent and a similar 30 percent drop in waste levels. Significantly, there has been a massive 95 percent cut in downtime on roll changes that occur every 30 minutes.”
Working 24/7,Robinette reportedly aims to replace 13 machines with four, by taking advantage of the greater efficiency that automation brings.