Bloomer Plastics Converts Custom Films
- Published: March 01, 2009, By By Edward Boyle, Contributing Editor
Bloomer, WI — population 3,500 — is home to three industrial parks, a golf course, four parks, an ice rink, and a 100-acre lake with a brand new beach and beach house. It is — as the town's website describes — the kind of place where “children can ride their bikes anywhere without fear.”
Nestled in this homage to small-town America is a manufacturer of custom converted and embossed films that converters around the world turn to time and again — not for the quaint atmosphere but rather for the quality products. In fact, this year Bloomer Plastics supplied more than 32 million lb of film to customers as far away as Europe and Asia.
While the company may not be one of the largest film suppliers in the world — heck, it's not even the largest employer in Bloomer — it has grown and thrived for the past 37 years, seemingly for the same reason as the town for which it was named: It gives people something they just can't seem to get anywhere else.
Filling a Void
Founded by Don West, a former engineer for a large film converter, Bloomer Plastics initially set out to service custom niche markets requiring embossed polyolefin films for industrial applications. Part of the reason for Bloomer Plastics' success — in fact, the reason the company was founded — is both its ability and willingness to deliver relatively small-sized runs to some otherwise high-volume industries.
At the time Bloomer Plastics was established, “If you didn't do multiple truck loads, the big film suppliers weren't doing business with you,” explains Neil Lundgren, president and general manager. “Since Don West started the business, we've taken the approach that we tailor our products to our customers' needs, so we often do smaller-than-truckload size.” Bloomer's versatility allows the company to complete multiple truckload orders but maintain a minimum order size of only 500 lbs.
“A big part of that was our ability to come up with solutions for our customers that they weren't able to get from the major film suppliers,” notes Lundgren, “and a part of that is the converting and laminating we do for them.”
Unique Products
Even today, every order Bloomer converts is custom, and the average size is just 6,000 lb — as little as four pallets of film. “Every product we make is unique,” says Lundgren. Still, the company's average lead times are just 16 days, with a maximum of three weeks.
“When you look at most of the business we've acquired over the last four or five years,” says Lundgren, “we tend to get the business from major film companies. They may offer ‘Product A’ or ‘Product B,’ but we can fine-tune our product to meet the exact customer needs.”
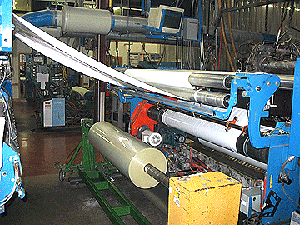
Bloomer's overall production capabilities include mono and coextruded cast films; polyolefins and their copolymers, including polyethylene (PE), polypropylene (PP), nylon, ethylene-methyl acrylate copolymer, ethylene vinyl acetate, acid copolymers, ionomers, ethylene vinyl alcohol, metallocenes, and other custom compounds. Markets served by Bloomer Plastics include packaging, graphic arts, protective films, automotive, metal protection, carpet, and textiles.
“Most of our current markets are continuing to grow, especially automotive,” says Lundgren, noting that Bloomer currently has some significant annual sales in the automotive market, which has dropped in the current economy.
Embossing Is Big
One of Bloomer Plastics' largest niches is the production of embossed films and sheets in thicknesses up to 70 mils; standard films are available from 0.9-mil to 40-mil. Bloomer converts film to 41-in. O.D., though standard rolls are 22 in.
The company offers more than a dozen emboss patterns, including matte, taffeta, diamond, frosted, dimple, linen, leather grain, diamond plate, polished, and woven. Materials the company can laminate to its specialty films include nonwovens, scrim, chopped fiberglass, fabric, sandwiching composites, ribbon lamination, and other substrates, including plastic.
To do so, Bloomer utilizes a range of converting equipment at its 80,000-sq-ft facility, including eight extrusion lines with heat laminating capabilities from Black Clawson, Davis-Standard, and Berlyn. Lundgren says cast embossed film increasingly is popular across all market segments because of specific advantages over blown film, including a more consistent film thickness, enhanced optical qualities, better dimensional stability, and contrasting directional properties in some applications.
Specifically, says Lundgren, embossing can alter the surface properties of films to meet particular converter needs, and gloss levels also can be varied to attain the desired effect. Embossing also provides a better anchor for coatings and offers superior release properties for many substrates.
“Embossed films add everything from a new decorative twist to the film or the packaging to efficiencies in filling and emptying the package,” says Lundgren. “There are a lot of benefits, and some of our customers are seeing there's a need out there where embossed film might help.”
Advantages of Vinyl Replacements
Another growth market for Bloomer is vinyl replacement films, which are manufactured to customer specifications. The film is manufactured with PE copolymers in thicknesses of 1.5-30.0 mil and widths up to 84 in. and available in a wide variety of colors, including clear and natural. The company also can incorporate a number of functional additives, such as ultraviolet inhibitors, anti-static, biodegradable, and fire retardants.
Lundgren says Bloomer Plastics' vinyl replacement films offer many advantages over conventional polyvinyl chloride films. For example, PE films are lower density, giving greater coverage per pound. They do not contain chlorine, resulting in no dioxin or acid formation when incinerated, are recyclable, and heat sealable under a broad range of temperatures, and can be made to be biodegradable.
Growth in Laminations
Bloomer Plastics offers packaging films in a variety of resin and manufacturing combinations, including PP homopolymers, copolymers, and impact copolymers. Lundgren sees packaging, in particular, as one of Bloomer's strongest growth markets. Currently, that market accounts for a growing percentage of its annual sales. In fact, he notes, “Our customers have driven us into more of a packaging mentality. Right now we're aggressively pursuing the protective film and packaging markets; doing laminations that include PET, metallized film, and foil laminations, even laminations of other people's films for their packaging,” he says. “A growth market for us has been with polypropylene. We offer a lot of different variations, different types of polypropylene. We're almost doubling the amount that we've shipped every year, so anybody who's using cast or blown polypropylene for packaging would have some interest in us.”
Contributing Editor Edward Boyle, based in Reading, PA, has covered the converting industry for more than 24 years. Contact him at EJB Communications; 610-670-4680; This email address is being protected from spambots. You need JavaScript enabled to view it..
Converter Info
-
Bloomer Plastics | 1710 N. Industrial Dr., Bloomer, WI 54724 | 800-638-0479 | www.bloomerplastics.com
Energy-Saving Solution
Bloomer Plastics' management team prides itself on its customer service. Neil Lundgren, president and general manager, says one recent example of its problem-solving abilities was for a “tier one company” that was using an adhesive film in their production process.
The customer previously purchased film from Bloomer and shipped the rolls to a converter that would then heat the film in an oven, apply the substrate, reheat it, and then laminate it to yet another product. That multi-step process proved inefficient and costly.
“We basically now complete all of those steps in-line for the customer,” explains Lundgren. “We were able to save them the extra shipping costs to the in-between converter, and the extra energy costs of having to reheat the film. And because you're not reheating the film, it's as strong as it's ever going to get right when it comes off our line.
“Every time you reheat film, it loses some of its characteristics, so we're able to give them a better product.”
Tools of The Trade
Additional converting machinery at work in Bloomer Plastics' Wisconsin facility includes the following equipment and accessories:
-
Beringer screen changers | Dynisco | www.dynisco.com
PFFC-ASAP 326 -
Blender | CRG Logics Inc. | www.crglogics.com
PFFC-ASAP 327 -
Blenders | Process Control Corp. | www.process-control.com
PFFC-ASAP 328 -
Dies | Cloeren Inc. | www.cloeren.com
PFFC-ASAP 329 -
Dies | Extrusion Dies Industries | www.extrusiondies.com
PFFC-ASAP 330 -
Edge detection | Ryeco Inc. | www.ryeco.com
PFFC-ASAP 331 -
Fiberglass chopper | Finn & Fram Inc. | www.finnandfram.com
PFFC-ASAP 332 -
Measurement & control systems | NDC Infrared Engineering | www.ndcinfrared.com
PFFC-ASAP 333 -
Pin perforator | Robert A. Main & Sons | www.ramsco-inc.com
PFFC-ASAP 334 -
Roll handling | Tilt-Lock | www.tiltlock.com
PFFC-ASAP 335 -
Slitting systems | Tidland | www.tidland.com
PFFC-ASAP 336 -
Surface treating | Pillar Technologies | www.pillartech.com
PFFC-ASAP 337 -
Web cleaning | Simco | www.simco-static.com
PFFC-ASAP 338 -
Web inspection | ISRA Surface Vision Inc. | www.isravision.com
PFFC-ASAP 339
Supplier Info
-
Black Clawson Converting Machinery | www.bc-egan.com
PFFC-ASAP 340 -
Davis-Standard | www.davis-standard.com
PFFC-ASAP 341 -
Berlin Extruders Inc. | www.berlyn.com
PFFC-ASAP 342