The RFID Buzz Gets Louder
- Published: November 30, 2005, By David J. Bentley Jr., Contributing Editor
PLC Probe
Are you old enough to remember the introduction of the transistor? It revolutionized radio by providing small, hand-held models you could take almost anywhere. Later, the microchip industry allowed the manufacture of computers that were much smaller than their “ancestors” but much bigger in capabilities.
Today, the buzzword in miniaturization is radio frequency identification (RFID). With the use of a very small device, it is possible to track almost anything, from lost children at Disney World to the location of a particular railroad car.
In flexible packaging, RFID has the potential to change completely the way suppliers, converters, and consumers use many items. RFID not only uses a small device, it also can transmit a great deal of important information. The bar code so common today for price scanning, inventory control, etc., soon may fall victim to its newer sibling—RFID.
RFID technology uses a computer chip containing considerably more information than a bar code can hold and can send this information using a small antenna within the chip. For flexible packaging, this means packages will “talk” by conveying information on their location, their expiration date, and similar items. The packages potentially will communicate with their suppliers and their consumers. Perhaps someday a piece of cheddar cheese in the refrigerator will ask a package of macaroni in the pantry, “Hey, let’s meet in a casserole dish in the oven for a hot time.” Silly? Sure. But the serious potential for packages to communicate in the future seems almost unlimited.
A practical example of RFID in flexible packaging involves obtaining data on all aspects of the supply chain. Suppose a supplier of polymer makes a batch of material. It goes to an adhesive manufacturer who compounds it into an adhesive, which then proceeds to a converter for use in a lamination. The laminate goes to a supplier who makes a package and fills it with product. With entry of the proper records into the data embedded in the chip, tracking this particular batch of polymer would be very easy, despite all these steps.
Resolution of flexible packaging problems could become simpler. In the example above, the converter that prepares the laminate would use certain lots of substrates and adhesives. A particular operator would be involved in running the laminator. The laminator would have certain settings for coating roll use, oven temperature, nip temperature, and the like. Laboratory results on a particular run could include coating deposition and bond values. All this could be in an RFID chip that accompanied the laminate to the next step at the food supplier. If something unusual happened further down the supply chain with the laminated material, vital information relating to the situation would be available immediately.
Although RFID is finding expanding uses every day, flexible packaging offers one advantage few other uses can claim: The chips are so small and inconspicuous that laminating them between two substrates is possible. In this way, they are safe and protected. If the substrates have ink coverage, the chips could even be hidden completely.
Why don’t we have extensive use of RFID in flexible packaging today? The first reason obviously is the cost. Somebody must pay for this, and nobody in the supply chain really wants to do so. The consumer does not want to pay either. Although the cost may only be a few cents per individual package, nobody wants to pay more for anything. As advances in the technology associated with RFID continues, the units will become smaller, better, and less expensive.
Another concern some people have is that RFID makes it easy for “big brother” to pry into their personal affairs. Some people might object to having the contents of their pantry, refrigerator, medicine cabinet, etc., available to outsiders.
Despite these drawbacks, RFID is coming to flexible packaging in a big way (think Wal-Mart!). Since it cannot be avoided, plan now how you will adapt and use this new technology. If you’re not a leader in this niche, you could wind up at the back of the parade.
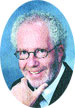
David J. Bentley Jr. is a recognized industry expert in polymers, laminations, and coatings with more than 30 years of experience in R&D and technical service. Contact him at This email address is being protected from spambots. You need JavaScript enabled to view it..