Seeking a Converting Superhero
- Published: June 30, 2005, By David J. Bentley Jr. Contributing Editor
PLC Probe
Not everyone can be Superman, but most people would like to be a hero. This column will tell the people who work in the flexible packaging and converting industries how to do that. Following is a look at some common wish list items people in these industries have expressed at various meetings in recent years. If you see something below you think you can accomplish or solve, you will be a hero.
Topping the wish lists for many people are lower-cost products. This is a tough wish to fulfill. Many materials used in converting and flexible packaging come from petrochemicals. As oil continues to become more expensive for one reason or another, the cost of many raw materials increases. To be a hero in this area, you will probably need to find alternate sources for raw materials. Perhaps taking a cue from Superman and using kryptonite would be a possibility.
Barrier films play an important role in flexible packaging today. People want films that provide higher barriers, have improved clarity, and are stronger. The rationale behind this wish is that such films could expand the number and types of items that could be available in flexible packages.
The best barrier film would be an invisible Superman—something with the ultimately highest strength and barrier that is perfectly clear.
A related topic is the need for high-performance films that will withstand retort conditions and offer higher heat resistance. Biodegradable films also are prominent on everyone’s list.
Polyester film is in common use today in flexible packaging because it offers many advantages, but it has one glaring shortcoming in the eyes of many users: It is impossible to heat seal. Thus, converters would love to have a heat-sealable polyester film. Development of such a film would negate the need to coat polyester film with heat-seal coatings or laminate it to a heat-sealable film such as PE. Using polyester film with all its inherent advantages then would be easier and less expensive.
Faster line speeds are important to many converters. Converting operations such as coating, laminating, extruding, etc., take time. Time is money. Being able to perform these converting steps more rapidly would offer some significant cost advantages. EB curing probably is the simplest and fastest converting operation in use today. Expanding the applications that could use EB curing might be one way to meet the desire for faster line speeds.
More consistent quality in substrates is something many people in the converting and flexible packaging industries feel is very important. When running paper, a plastic film, or a foil in a high-speed converting operation, a flaw in gauge control or an actual hole or tear can wreak havoc by causing a line break, with ensuing downtime that could last for hours. Variation across the web of a film also is a common problem. Difficulties with areas in which clarity and density vary within substrates usually result in the manufacture of some substandard material that must be removed from a finished roll of goods.
Some people actually wish they could have a replacement for foil because of its handling difficulties. This is an area that has been undergoing active development. Metallization of various plastic films is one approach that has found a certain amount of promise in foil replacement, but it is not the complete answer yet. Eliminating metal completely by using a film of a super polymer is the ultimate dream of many people in the industry.
Winding and slitting seem to have been problem areas since the beginning of the converting industry. This is evident by the many papers at technical conferences and the numerous seminars that address these topics, as well as the various machinery experts who travel the world to help people having difficulties in these areas. None of the difficulties mentioned so far is solved easily, but the problems in attaining perfect winding and slitting are perhaps the most difficult of all. So take your pick. Is there an area in which you can be a converting hero? If so, put on your cape and get started.
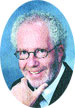
David J. Bentley Jr. is a recognized industry expert in polymers, laminations, and coatings with more than 30 years of experience in R&D and technical service. Contact him at This email address is being protected from spambots. You need JavaScript enabled to view it..