Flexographic Printing: Super Setup
- Published: October 01, 2010, By Edited by Claudia Hine, Managing Editor
Fifteen years ago, Envases Del Pisueña, located in the suburbs of Mexico City, started making shopping bags. Thanks to a dedicated print staff, the company grew and grew. Customers began asking for flexible packaging products, and in response, the company purchased its first press, a six-color Comexi.
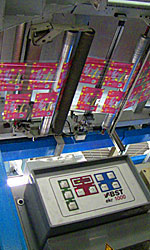
Then came a Flexotecnica, followed by a laminator, and then a slitter. With the growth came a seemingly constant stream of new machines and equipment to keep up with customers' needs.
Today Envases Del Pisueña specializes in candy wrappers and snack bags. It has grown to 47 employees running three shifts a day, seven days a week.
The facility houses four flexographic central impression presses, a stack press, two laminators, and four slitters. The company runs polypropylene (PP), biaxially oriented PP, polyethylene, and a little paper from time to time. Its newest press is a Uteco Emerald, installed about two years ago.
At the time, Envases Del Pisueña needed greater capacity in terms of the number of colors, machine speeds, and overall press value. According to Jesus G. Abascal, general manager, the Uteco press was selected because the company needed a machine that was strong, stable, heavy duty, and could be run 24/7.
The ten-color press runs all solvent-based inks and has BST web guiding systems on the unwind and the rewind. It features Rossini sleeves and Praxair anilox rolls and recently was retrofitted with a new BST Pro Mark print inspection system.
Pressure To Perform
The retrofit was initiated because of competitive pressures. Envases Del Pisueña wanted to optimize press performance while minimizing waste and downtime. “Our customers were asking us for shorter lead times, better prices, more critical color matches,” says Abascal. “We felt this was an opportunity to respond to our customers and improve our competitive position.”
Abascal consulted with Zol Plastics, a representative of BST Pro Mark in Mexico. The company recommended a Super HANDYScan 4000, with Smart Register and Automatic Color Monitoring. Says Abascal, “We needed to upgrade our inspection and quality control capabilities and were particularly interested in on-press color management and register control. We viewed this retrofit as an opportunity to improve our quality control and to optimize the productive capabilities of the press.
“We wanted to shorten the time to start a new job and to reduce the time and material used to set register. The Super HANDYScan has played a big role in allowing us to meet that goal. We have actually cut [startup time] in half from our other machines, so we are very happy with that.” The system has a “Smart Register” function, which allows setting register with no special marks, using existing plates and existing artwork, and adjusts register even when the press is not running.
On-press color management was another goal the new system met. “We are using the automatic color monitoring capability on just about every job. It allows us to easily hold color within two Delta E with minimal effort, and the results are entirely consistent with our X-Rite [color measurement] unit. It is a very reliable system for color management and has helped us a lot,” Abascal says.
He also has seen improvement in other areas. “We are producing more on this press now than ever. Since the Super HANDYScan was installed, we have increased our average running speed from 150 meters per minute to 200 meters per minute.”
There has been a reduction in returns from customers, which he attributes to the improved quality control. “Not long after the Super HANDYScan was installed on the press, our customers noticed the difference in our quality. They began asking what we were doing differently and what we had changed. So we brought them in and showed them.” The on-press inspection system has become a marketing tool, helping the company strengthen relationships with existing customers and even finding new ones.
Converter Info
-
Envases Del Pisueña | 1a Sur 4 S/n, Col: Independencia, Tultitlán De Mariano Escobedo, Mexico 54914 | +55 5894-0694
Supplier Info
-
Comexi | www.comexi.com
Circle 301 or visit www.freeproductinfo.net/pff -
Flexotecnica | www.flexotecnica.it
Circle 302 or visit www.freeproductinfo.net/pff -
Uteco | www.uteco.com
Circle 303 or visit www.freeproductinfo.net/pff -
BST Pro Mark | www.bstpromark.com
Circle 304 or visit www.freeproductinfo.net/pff -
Rossini | www.rossini-na.com
Circle 305 or visit www.freeproductinfo.net/pff -
Praxair Inc. | www.praxair.com
Circle 306 or visit www.freeproductinfo.net/pff -
X-Rite | www.xrite.com
Circle 307 or visit www.freeproductinfo.net/pff