Is Gravure Coating Right for You?
- Published: February 10, 2020
By Ted Lightfoot, Contributing Writer
Most people who read articles on coating have products they want to coat or coating machinery they want to utilize. Gravure coating is a robust coating method, but it does some things better than others. Both groups of readers can benefit from a realistic assessment of how well a given product will run on a gravure coater.
Gravure refers to the use of engraved rolls to control how much coating is delivered to the web. Figure 1 shows common engraving patterns. Open cells are easier to clean and give thicker coatings; closed cells often give better coating quality. Figure 2 shows the common arrangements of engraved rolls, backup (or impression) rolls and offset rolls. In direct gravure, the web passes between the engraved roll and the backup roll. Both rolls travel with the web. In reverse gravure, the engraved roll shears against the web. With offset gravure, a rubber roll transfers the coating from the engraved roll to the web in a second nip. Kiss coating –without a backup roll—is the simplest configuration but cannot run at high speed. With reverse, kiss, and differential offset coating the ratio of the gravure and offset rolls to the web speed controls the coating weight.
Gravure can coat liquids with Brookfield viscosities from a few to several thousand centipoise (cP) at wet thicknesses from submicron to over 2
00 microns. Gravure is relatively robust to non-Newtonian behavior and has been run at speeds up to 3000 fpm. But those capabilities are not independent and not applicable to all products or configurations.
The substrate, the coating (including solvents) and the behavior of the coating impact the suitability of gravure coating. Solvents can attack the rubber rolls and dry on the gravure roll leading to precipitation in the cells. MEK and IPA are the most volatile common gravure solvents; more volatile solvents present challenges in drying on the roll and managing fumes in the coating room. In most cases the cells of the gravure roll are not completely empty when they leave the nip and precipitation is most problematic between the nip and the bath. Lubricity is helpful for the high shear configurations; abrasive materials can cause excessive wear.
The rheology of the coating also matters. Most people measure viscosity with a Brookfield or cup viscometer. These measure low shear viscosity. But the shear in the coating nip can be very high –thousands of reciprocal seconds-- and high shear viscosity (e.g., measured with an ICI cone and plate viscometer) is more important in determining how something will coat.
Gravure coating evolved from gravure printing and works well for coatings that behave like printing inks. Ink viscosity drops under high shear (shear thinning) and stays low for a while after being sheared (thixotropy). Gravure is quite tolerant to these behaviors. Neither shear thinning nor thixotropy is required for gravure coating but they affect the quoted range of acceptable viscosities. The limit for low shear viscosity is in the thousands of cP, but coatings that work well for even moderate speed gravure coating typically have high shear viscosities below 100 cP.
Gravure printing and coating work well with paper. However, printing deposits discrete dots of ink that do not spread on the substrate; with coating the dots must spread to give a uniform coating. Paper can wick the coating out of the roll leaving a replica of the engraving pattern rather than a uniform coating. Offset gravure gives the coating a chance to level and be smeared in the secondary nip: this is a good choice for paper.
Both direct and reverse gravure coating are widely used for film coating, although baggy webs pose problems. Gravure printing and direct gravure coating of foils is common; however, foils constrain the backup roll pressure. Reverse gravure is sensitive to oil on incoming foil.
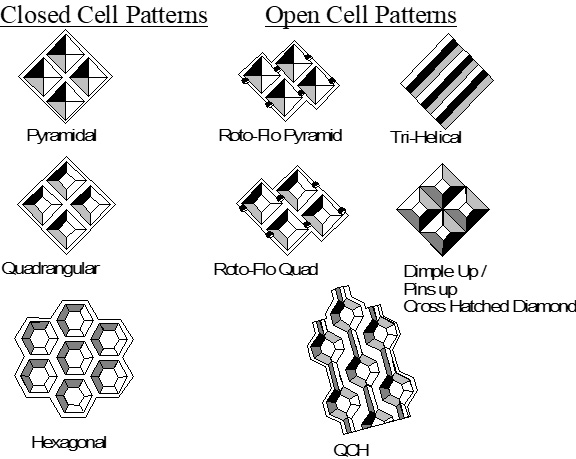
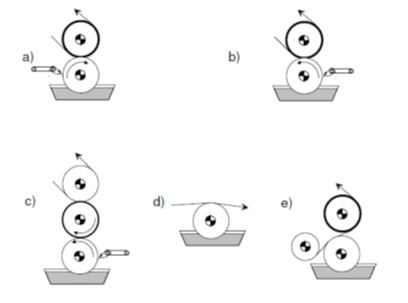
About the Author:
Ted has worked in coating, drying, laminating and film casting for over 35 years. His experience in R&D, plant support, as a Six Sigma Black Belt for Growth, and application development (helping customers develop processes and products) has taught him how strongly raw materials and processing affects product performance. He is a consultant , writer, speaker and gives short courses on coating and drying he can be reached at This email address is being protected from spambots. You need JavaScript enabled to view it..
While gravure is attractive for many applications, the only way to prove it works is to try it. But coating trials are expensive and failed trials burn political capital with customers. These guidelines should help develop realistic expectations of how well gravure will work for a given product to help product and process people prioritize their scale-up work.