Color 101: Part II
- Published: February 01, 2007, By By David Argent Contributing Editor
Process Management
Last month we discussed control of raw materials, and now we look at a simple check list of procedures required for color measurement and control. If any of these are missing or are suspect, the result will be waste and failure.
1. An ink proofing method correlated to the press has been established. This ensures proofs accurately predicting press color can be made in the lab for initial color approval and subsequent ink batch control.
2. An approved physical color target exists. Ideally, the final approved color target is from the production press using all specified inks and substrates and is signed off by the consumer product company. For future use, this target should be stored protectively, away from light and in stable temperature and humidity.
3. Color measurement devices are used, typically spectrophotometers. Use of a spectrophotometer is recommended throughout the process—for numerically defining the target, measuring the proof, controlling ink batches, and verifying color throughout the press run.
4. Numeric color targets are used with process- based tolerance. The values in this chart are for a bright red proofed in the ink room. The tolerance values are <1, meaning the samples are a good visual match. On the press it usually is possible to achieve a match within a DEcmc of 1. Tolerancing is a balance between color quality and waste generation. A narrow tolerance, say a DEcmc of 0.5, is not visually perceptible and is achieved on the press only by constant adjustment and possible culling of output. The lesson here is not to set color tolerances beyond the capability of the press.
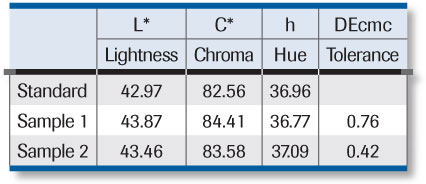
5. Documented and fixed press conditions. This will ensure new press runs can be completed with minimal waste.
6. Sampling and conformance procedures are in place. Many consumer product companies want self-inspection reporting from the converter with statistical data on color conformance and trends. Spectrophotometer software often will have these features built into the database.
A few last thoughts: Some converters embracing numeric color control are using the data collected to optimize press operation in creative ways. For instance, manipulation of L* readings (which correlate to ink film thickness) can improve ink mileage significantly while keeping the color within spec. Also, it is possible to “preflight” the color in the ink blending operation so the batch falls within color spec on the press during startup. This preflighting allows for color shift due to viscosity thinning at startup.
Even with all these controls, bad things continue to happen to good colors—see next month’s column for more on this topic.
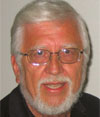
David Argent has 30+ years of experience in the converting industry. He specializes in process analysis and improvement with particular emphasis on ink and coating design and performance. Contact him at 636/391-8180; This email address is being protected from spambots. You need JavaScript enabled to view it..