The Rx for RH
- Published: August 31, 2004, By Pierre A. Husson, Husson Inc.
Remember the converting problems you had last winter? Reducing them this year might be easier than you think.
Converters commonly face heating season problems caused by dry air. These problems include sheet separation, misfeeds, warping and dimensional changes, ink coverage maladies, folding and gluing problems, and warehousing issues. These problems affect press and die-cutting speeds, run time, overtime, paper waste, and quality — all of which cut into profits.
If you carefully investigate the converting problems you had last winter, you'll learn that reducing these problems can be easy. Usually it's not expensive, return on investment is fast, and the fix is usually permanent.
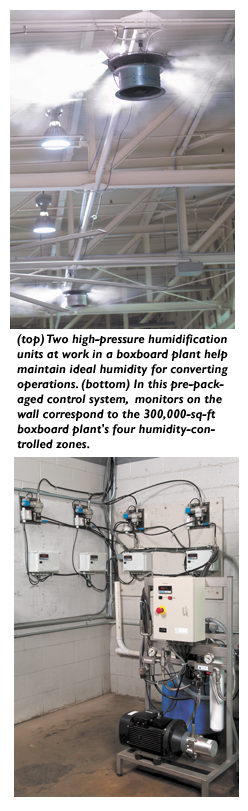
Humidity Problems Often Misdiagnosed
Since many dry air problems are seasonal, managers often misdiagnose causes, blaming a bad batch of substrate, machinery problems, or other year-round problems for problems caused by a loss of humidity.
Maintaining proper relative humidity (RH) through the entire cycle of transportation, storage, sheeting, coating, printing, die-cutting, and finishing will have a substantial impact on the moisture content of the materials you coat, print, and finish.
Heated indoor air in plants often is desert dry in winter, with RH often dropping to less than 10%. Ideal humidity for converting is 45%-55%, at a temperature of 68-72 deg F. It is hard to maintain this level of humidity in heated winter air, and in most plants, adding moisture to the air is necessary to reduce production and quality problems and improve indoor air quality.
Sheet separation and misfeeds occur when dry air (less than 40% RH) causes stock to become charged with static electricity. The sheets stick together, and the sheet feeder can't separate them. The press takes the double sheet. The results aren't pretty!
Edge tightening and curling is caused by loss of humidity on uncovered edges of stored stock. Grippers find it almost impossible to pull the paper through the press. Sheets fold and jam, causing slower press speeds, work stoppages, extra cleanup, and waste. Once edge tightening has occurred, it is virtually impossible to correct. Edge tightening also can cause unsightly wrinkles in stock, which causes waste.
Dimensional instability affects the sheet as a whole but is usually more severe in the width, leading to problems in registration and die-cutting. For instance, a change in width of just 1 mm in 1 ft can lead to registration problems of almost five halftone dots. Dimensional changes also can mean sheets are too small for dies, requiring reworking or replacing dies or excessive waste.
Sucking up fountain solution can be a problem. In offset printing, dry paper sucks up fountain solution, slowing the drying process. Printers with severe low humidity often need to supply 10%-20% more fountain solution daily, leading to frequent resettings and inconsistent print quality.
Ink problems are common. As dry stock sucks up excessive ink, uniformity is lost, quality suffers, and ink costs can go sky high. Result: More stops, more tweaking and adjusting, plus problems with waste, on-time delivery, overtime, and cost control.
Flexibility and foldability in the die-cutting and finishing area also can be affected adversely, as can gluing, leading to rejects. Stock is most flexible and pliable at 50%-65% RH. Dry, brittle stock often cracks during scoring, cutting, and folding, causing waste and releasing dust. Glue application and results can become inconsistent. Sometimes managers think they have a stock or glue problem. Smart ones know they have a humidity problem.
Transportation and Storage
As they come from the mill, paper and board contain 5.5%-10.5% water. Since moisture migrates to the driest area in the vicinity, stock absorbs or releases water depending on relative humidity. Its humidity balance begins to change from the minute it leaves the mill.
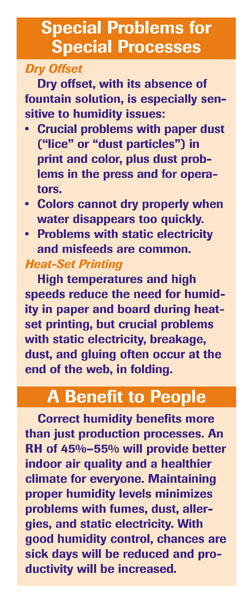
It is important to make sure stock does not get out of humidity balance and begin changing dimensions in transit or in your paper storage area. Once the damage is done, it is frequently impossible to correct it. Store stock as close to “mill conditions” as possible. If it comes wrapped, leave it wrapped. The optimum temperature range for storage is 68-72 deg F, with RH at 45%-55%.
When air is heated, humidity levels drop and suck the moisture out of stock. RH levels under 30%-40% are usually low enough to cause problems. In most cases, water must be added to the air to keep humidity at desirable levels. For instance, maintaining 50% RH at 70 deg F requires four times as much water in the air as at 32 deg F.
Paper and paperboard quickly get into equilibrium with their surroundings, ranging from minutes for small amounts to a couple of weeks for pallet loads. Use stock as quickly as possible after it is unwrapped.
A Simple Solution
These problems can be avoided by maintaining proper temperature and RH in your warehousing and storage areas, prepress, pressroom, die-cutting, and finishing areas.
Manufacturers have developed a wide array of technologies and products aimed at solving humidity problems. Each type converts water into fine droplets that are evaporated into your plant's air.
In general, the smaller the particles, the faster and more efficiently they increase RH. Virtually any of the leading technologies can provide adequate humidification to solve problems. But not all methods are “created equal” in every situation. Each method has its strengths and weaknesses in terms of cost, efficiency, and effectiveness.
It is important to use clean, soft water in your system. Depending on the water quality in your area, it also may be necessary to look into conditioned or reverse osmosis (RO) water.
Steam systems produce very fine droplets (0.3-1.0 microns) that evaporate quickly and effectively. But all steam systems also produce heat. Most plants don't need the added heat!
Today most steam systems are “electric steam,” using electricity to heat water. Since electricity is a high-cost source of heat, electric steam humidification usually has by far the highest energy costs. Maintenance costs to prevent buildup of corrosive residues on heating elements also are high.
Centrifugal systems use centrifugal force to atomize water. Units have low installed costs and relatively low operating costs. However, this technology creates larger droplets that don't evaporate as efficiently, sometimes leading to excessive condensation problems and wetness. Concerns about air quality and health also have been raised over open water baths used in centrifugal systems, which may promote bacteria growth.
Ultrasonic humidifiers use high-frequency electricity to break droplets away from the surface of a shallow water bath. Ultrasonic systems are more energy-efficient than steam or centrifugal humidifiers, although, again, air quality and health concerns have been raised over bacteria in open water baths.
Compressed air systems use air at high velocity to convert water from a nozzle into fine droplets. Since no heat is involved, energy costs are lower, as are maintenance costs. However, in many work areas, the high-pitched sound from nozzles can be annoying to employees, so they are best used where they need not be placed close to workstations.
High-pressure humidifiers use a high-pressure electric pump to drive RO water through a fine nozzle at pressures of 900-2,000 psi, creating a fine mist or “fog” of droplets averaging about 10-15 microns in diameter. Since no heat is required, this is an inherently energy-efficient method. Installed cost is much lower than steam or compressed air systems. Noise is not usually a problem.For most printers, the biggest selling points for high-pressure humidification are low maintenance costs and very low operating costs due to energy efficiency. For example, energy costs for high-pressure systems are typically about 15%-20% those of compressed air systems and less than 1% those of electric steam systems.
The greatest shortcoming of high-pressure systems is their fog requires a longer distance to evaporate than some other methods. This can be overcome, simply and easily, by use of a system with a built-in fan. Units with fans distribute moisture with greater uniformity throughout the area. A built-in fan also allows high-pressure systems to work effectively in spaces with ceiling heights as low as 8 ft, without any drain water.
If you take a hard look at the production problems you had last winter, you'll find many were caused by dry air. Luckily, through the many methods of humidity control available to you, the solutions can be simple, fast, and relatively inexpensive.
Pierre A. Husson is president of Husson Inc., Sturtevant, WI, USA, the exclusive US sales, engineering, and service arm of ML Systems, a European manufacturer of high-pressure humidification systems with more than 150 installations in the US and more than 2,000 worldwide. Pierre can be reached at 262/884-4669; This email address is being protected from spambots. You need JavaScript enabled to view it..
The views and opinions expressed in Technical Reports are those of the author(s), not those of the editors of PFFC. Please address comments to author(s).