Product Protection
- Published: March 01, 2007, By By Steve Sargeant and Ken Chang, Toray Plastics (America)
Barrier Films
Manufacturers of perishable products are well aware that a later “sell by” date on a package can affect a customer’s decision to purchase one brand instead of another. Even if the shopper has made up his or her mind which brand to purchase, there is a natural tendency to look behind rotated stock for the package with the latest “sell by” date, leaving ones with earlier dates on the shelf to become even less desirable.
The problem is exacerbated by the growing movement to eliminate partially hydrogenated vegetable oils containing trans fats—routinely used to extend shelf life—from products such as fried snacks, baked goods, and confections. Many of the edible oils used as trans fat replacements are more sensitive to moisture and oxygen than the fats they replace. This means if the packaging for the reformulated product does not have better moisture vapor- and oxygen-barrier properties than the packaging for the product containing trans fats, the “sell by” date will have to be even shorter, so an even greater risk for loss of profit is created.
In order to achieve low moisture vapor and oxygen transmission rates and extend the “sell by” date of perishable products as long as possible, consumer product companies and converters generally use polyvinylidene chloride (PVDC)-coated polypropylene (PP), barrier metallized PP, or aluminum foil lamination packaging constructions.
Indeed, among the three choices, a flat sheet of aluminum foil is essentially impenetrable by moisture and oxygen, as both its moisture vapor transmission rate (MVTR) and its oxygen transmission rate (OTR) approach zero. However, when packages made with foil are subjected to the repeated manipulation and handling that are common with manufacturing, cartoning, shelf stocking, and consumer handling in the retail environment, they can develop pinholes and become permeable. They also can develop permanent creases and wrinkles, making the package appear older and more “shopworn” than it really is.
Traditionally, PVDC-coated oriented PP (OPP) film has been specified for demanding applications because of its unique combination of mechanical, barrier, and esthetic properties. However, it is expensive because of its two-step manufacturing process and its higher density, which results in lower yield. In applications requiring either moisture- or oxygen-barrier properties, but not both, use of either foil or PVDC can lead to over-engineering. There are also environmental issues with PVDC. Mounting global pressure about the use of halogenated materials in traditional plastics applications is driving a desire to remove PVDC from packaging applications and replace it with an alternative that offers the same or improved performance at similar economics.
OPP Developments
Today, industry developments in coextruded OPP film technology offer end-users and converters new value-added options for “ultra” barrier protection. New ultra-high-barrier metallized OPP technology has moisture- and oxygen-barrier properties approaching those of foil. In fact, some of the industry’s new, advanced metallized films provide approximately 100x the oxygen barrier of previous generations of metallized films. This allows food manufacturers not only to gain the advantage of later “sell by” dates but also to realize the economies of more flexible manufacturing cycles, because when dates are later, store shelves do not have to be restocked as often.
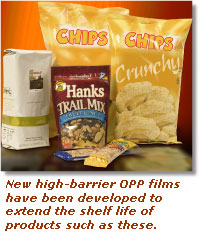
Also important is the development of high-barrier clear film technology that offers significant oxygen-barrier properties, although not moisture-barrier properties, comparable to those of conventional metallized films, presenting end-users and converters with more package manufacturing options. (It should be noted the ultra-high-barrier and high-barrier films’ technologies are considered by film manufacturers to be proprietary.)
Both the new metallized and clear barrier films available today maintain their outstanding barrier properties as flat laminated films and when formed into flexible packaging. Because of their unique barrier properties, they can be used not only in food product applications, especially those being reformulated to eliminate trans fats, but also for packaging pet food as well as for agricultural, chemical, and medical applications. Thus they open the door to even more business opportunities.
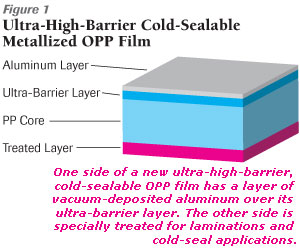
Ultra-High-Barrier, Cold-Sealable Metallized Film
The ultra-high-barrier, cold-sealable metallized film technology is a biaxially oriented film that is vacuum-deposited with aluminum on an ultra-high-barrier layer and treated on the other side for laminations and cold-seal applications (see Figure 1). It is designed for use as either an inner web of a lamination with converter-applied cold seal or as the middle ply of a multilayer lamination where it provides exceptional oxygen- and moisture-barrier properties. It is ideally suited for gas-flushed applications.
A comparison of moisture-vapor and oxygen-transmission rates for the ultra-high-barrier, cold-sealable film (UHBF) as compared with a metallized OPP film is shown below.
Moisture Vapor Transmission vs. Oxygen-Transmission Rates of Barrier Films | ||
---|---|---|
Barrier Film | MVTR @ 100 deg F, 90% RH g/100 in.2/day | OTR @ 73 deg F, 0% RH cc/100 in.2/day |
Metallized OPP | 0.010 | 1.5 |
UHBF (Cold Sealable) | 0.010 | 0.003 |
UHBF (Heat Sealable) | 0.010 | 0.003 |
MB PVDC | 0.27 | 0.95 |
HB PVDC | 0.16 | 0.30 |
HBF (Heat-Sealable Clear) | 0.19 | 0.67 |
Typical laminated structures in which a new UHBF might be combined with polyethylene (PE), polyethylene terephthalate (PET), biaxially oriented PP (BOPP), and other materials include the following:
- PET/Ink/PE/UHBF/PE
- BOPP/Ink/PE/UHBF/PE
- Ink/Paper/PE/UHBF/PE
- Outer Layer/Ink/Board/PE/UHBF/PE
- Outer Layer/Ink/UHBF/PE-Board/PE
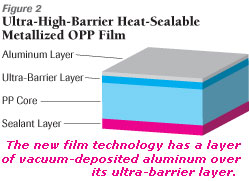
Ultra-High-Barrier, Heat-Sealable Metallized Film
The ultra-high-barrier, metallized film is a biaxially oriented film that is vacuum-deposited with aluminum on an ultra-high-barrier layer and is heat-sealable on the other side (see Figure 2). It is designed for use as an inside sealant web and provides moisture and oxygen barrier for gas-flushed applications. End-users and converters can expect superior formed-bag durability to be maintained after the package is made. It offers superior light protection with a minimum optical density of 2.0, as well as excellent hot tack and a wide heat-seal range.
See the table for a comparison of moisture-vapor and oxygen-transmission rates for the ultra-high-barrier, heat-sealable film (UHBF) as compared with a metallized OPP film.
Typical laminated structures in which this new UHBF might be combined with heat-sealable transparent OPP, heat-sealable PE or an adhesive (Adh), and other materials include the following:
- OPP/Ink/PE or Adh/UHBF
- Outer Layer/Ink/UHBF
- Outer Layer/Ink/Paper/PE/UHBF
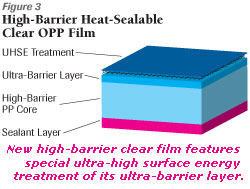
High-Barrier Clear Film
The high-barrier clear film technology consists of a BOPP film featuring ultra-high surface energy treatment of its ultra-high-barrier layer on one side and heat sealability on the other side (see Figure 3). Designed for use as an inside sealant web, it provides high oxygen barrier and exceptional moisture barrier. This new film technology also offers improved oil resistance, increased puncture resistance, and better stiffness. With its outstanding oxygen-barrier properties and its suitability for gas flushing, it is an excellent alternative to PVDC-coated OPP.
A comparison of moisture-vapor and oxygen-transmission rates for the high-barrier, heat-sealable clear OPP film as compared with moderate-barrier (MB) and high-barrier (HB) PVDC-coated films is shown in the table.
Typical laminated structures in which this UHBF might be combined with OPP or BOPP, PET, PE or Adh, and other materials include the following:
- OPP/Ink/PE or Adh/HBF
- BOPP/Ink/PE or Adh/HBF
- PET/PE or Adh/HBF
- Outer Layer/Ink/HBF
SUPPLIER INFO:
Toray Plastics (America)—PFFC-ASAP 312. torayfilms.com
Steve Sargeant Ph.D. is director, new business development, at Toray Plastics (America), North Kingstown, RI. Reach him at This email address is being protected from spambots. You need JavaScript enabled to view it.; 401/294-4511, ext. 4442. Ken Chang, director, new product development, can be reached at This email address is being protected from spambots. You need JavaScript enabled to view it.; 401/294-4511, ext. 3227.
The views and opinions expressed in Technical Reports are those of the author(s), not those of the editors of PFFC. Please address comments to author(s).