Drives Retrofit: More Space, Less Power
- Published: June 01, 2010, By Edited by Claudia Hine, Managing Editor
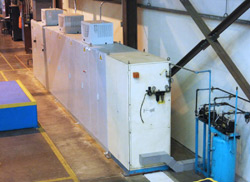
Plans to expand slitting capacity at Applied Extrusion Technologies (AET) began last year with the upgrade of an aging 8-m-wide Atlas CW982 AP primary film slitter, originally installed in 1989 at AET's production facility in Terre Haute, IN. A highly intensive 18-day schedule included a major overhaul of the obsolete control system by several Atlas engineers with support from AET technicians on site.
“This upgrade was a very impressive project by the team of Atlas engineers who did a really professional job for us,” says Brad Roush, controls specialist at the plant. “We have reduced the 22 original electrical control panels to only seven, making a lot more space but, more importantly, also dramatically reducing our power consumption. All the old transformers have been taken out and replaced with active dynamic drive technology. The machine is now so much more efficient, reliable, and productive.”
Today the Atlas slitter has all AC web drives throughout as well as new rewind arm positioning and automatic knife positioning systems, which enable quicker changeovers between production runs and much less machine downtime. The control desks for the unwind and rewind side of the machine have been replaced and upgraded with new PC and PLC technology, making the slitter more user friendly and easier to operate, with a vast data storage facility.
“We can now run the slitter at 3,300 feet per minute, compared to 2,000 feet per minute previously, but also with much better roll quality,” Roush says. “Basically, there is nothing wrong with the mechanics of the machine — I think it will run forever! It was just that the original spec of the slitter could not keep up with the demands of today's BOPP [biaxially oriented polypropylene] film production requirements.”
AET has six other Atlas primary and secondary film slitters, all installed during the 1990s, including a machine commissioned in 1998 that is 33 ft (10 m) wide. Upgrades to some of these machines will be carried out by Atlas later this year and into 2011.
“The 18-day project has been a huge success for AET Films,” confirms Lawrence Mauer, director of operations at the Terre Haute facility. “We had no problems during the upgrade and checkout. We were able to fully accept the upgrade as soon as work was completed. In all, it has been a rewarding and important step toward a more sustainable solution for the company.”
Supplier Info
-
Atlas Converting Equipment-Bobst Group | www.bobstgroup.com/atlas
Circle 316 or visit www.freeproductinfo.net/pff
A Global Reach
Established in 1986 with its initial operations in Middletown, DE, Applied Extrusion Technologies (AET) manufactures specialized oriented polypropylene (OPP) films and serves some of the world's largest consumer product companies. AET offers more than 80 product groups, including holographic films for promotional packaging and board lamination as well as barrier films and heat-sealable films used to protect snacks, cheeses, meats, fresh produce, fruit, and candy bars.
Rapid expansion of its business, including several strategic acquisitions, has led AET to focus on the development, manufacture, and marketing of a wide range of OPP films to a worldwide marketplace. In addition to its Terre Haute, IN, plant, the company has a production facility in Varennes, QC, Canada.
Converter Info
-
Applied Extrusion Technologies Inc. | US Highway 41 N., Terre Haute, IN 47805 | 812-466-4277 | www.aetfilms.com