A Bunch of Hot Air
- Published: April 30, 2006, By Neil I. Steinberg, Somerset Engineering
Dryer Technologies
Web dryers actually are fairly simple process machines despite an apparent myriad of design options. So what causes most of the headaches that we in the web process industries suffer? Four problems: the wrong heating system, lousy instrumentation, not enough zones, and pushing the dryer beyond its design limits.
The major dryer types are air impingement, parallel flow air, infrared (IR) radiant, and other radiation. The heating mode pretty well describes the type of dryer; mechanical construction is, with infrequent exceptions, secondary. Air flow (or inert gas in the case of some solvent dryers) is required with all designs to remove the moisture.
Web Drying Process Overview
The web drying curve—web surface temperature plotted vs. distance downstream from the dryer entrance—is a good general depiction of the drying process. Figure 1 shows four separate regimes that we usually want to match with the zones in our dryers.
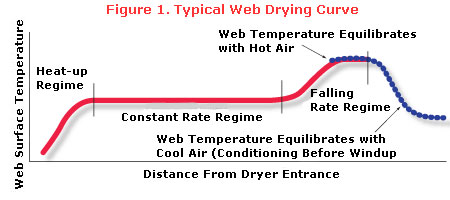
We’ll start with the second or constant rate regime, because that is where most of the drying happens. A good approximation for impingement dryers is: The web temperature is close to the wet bulb temperature of the impingement air. In parallel flow dryers and some radiant dryers, the air temperature and humidity change in the machine direction, so the web surface temperature and the drying rate are not quite constant.
In the heat-up regime, the wet web starts at room temperature and zero drying rate and approaches the temperature and drying rate of the constant rate regime. In the majority of cases, most of the heat is absorbed by the substrate.
After most of the moisture is driven off, drying slows and the web surface temperature rises. This is the falling rate regime. If the dryer is long enough, the web eventually will equilibrate with the air temperature. As in the heat-up regime, most of the heat usually is absorbed by the substrate.
The final regime or portion of the process is the conditioning regime, in which we equilibrate the web with room or storage temperature. It isn’t really part of the drying process and is only significant if we intend to use or sell the coated web. A hot web will try to shrink after winding with very bad results. At best we can expect an assortment of flatness defects. At worst the web gradually can crush the windup core.
Matching the desired drying curve requires many independently controlled drying zones. If there aren’t enough zones, the portion of each zone with the lowest tolerance for high temperature, low humidity, high air speed, etc., limits the drying rate in that zone. For example, if the wet coating is disturbed easily by high impinged or parallel air flow, the whole zone is limited to conditions the start of the process can tolerate.
Air Impingement
Multiple-nozzle, multiple-zone air impingement (including flotation) is the most efficient and flexible forced air design. It is also very cost-effective and often can be combined with IR radiant heat to increase capacity in a limited space or in an existing unit.
In air impingement dryers, transversely mounted air nozzles or slots blow plane transverse air jets perpendicular to the web on one or both sides (see Figure 2).
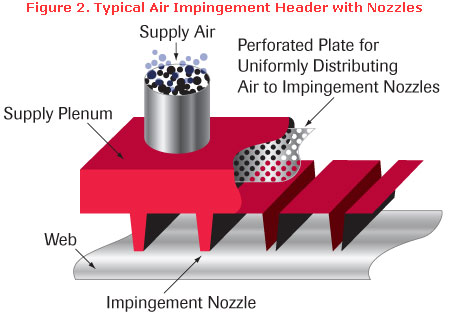
There are designs that use perforated plates instead of slots or slot nozzles. While they offer slightly better heat transfer efficiency, they are very prone to streaks and coating disturbances.
Impingement nozzles are supplied with air individually or in groups. This allows for fairly elaborate zoning so the temperature and humidity of the air the wet web sees can be controlled in the machine direction. In many cases, radiant heaters can be mounted above the web between nozzles. Radiant heaters below the web are not a good idea.
The flotation dryer is a particularly interesting variation on air impingement. Nozzles are mounted facing both sides of the web, and boundary layer effects suspend the web in a serpentine path between the nozzles. When combined with air bars for turning the web, this allows for fairly long web paths without wet side contact in a confined space. The serpentine path also suppresses machine direction tension wrinkles. Flotation dryers are a bit less efficient than optimally designed impingement units, but the web transport advantages often offset this minor loss.
Parallel Flow Forced Air
Parallel flow forced air is inefficient and inflexible, and a parallel flow air dryer really is acceptable only under two conditions: You already own it so you might as well use it, or it’s an add-on unit with an existing dryer to better use an open web path before and/or after the main dryer.
A simple parallel flow dryer consists of a web moving through a duct or tunnel with forced air flowing in the opposite direction (countercurrent) or in the same direction (cocurrent) as the web.
In countercurrent operation, dry, warm air flows into the web exit and travels along the web in the opposite direction to web flow. The air gradually picks up moisture and cools. The warmest, driest air sees the warmest, driest web. The spent wet, cool air sees the wet web at the dryer entrance. This means there will be significant heat transfer to the web and the potential for drying all along the web path.
In cocurrent operation, the warm, dry air and wet web enter the dryer in the same direction and gradually equilibrate with each other. This means the drying process gradually can slow down and even stop before the web exits the dryer.
There really is only one practical way to divide a parallel flow dryer into zones: Operate several parallel flow units in series.
Infrared Radiant Drying
Radiant (IR) heating is far more powerful and less expensive than forced air, but the heaters must overlap the wetted web on each side by at least one heater-to-web clearance. Machine direction zoning is easy: Just divide the heaters into separately controlled banks. Air flow is required to remove the moisture.
Be sure the heaters overlap the edges of the wetted web by at least one heater-to-web clearance, or the edges of the coating will not dry fast enough.
Other Radiant Drying Systems
The more exotic radiation systems (microwave, radar, radio frequency, etc.) are great when the radiation couples to the solvent. They are pretty good when it couples to the coating solids. These conditions avoid or reduce overheating uncoated substrate. Radiation that couples significantly to the substrate is a waste of money (IR is a lot cheaper) and can be real trouble if the coupling efficiency increases with temperature, a not-uncommon problem. Remember to provide some forced air to remove the moisture. A web moving in a duct is a drag pump but not a good one.
Instrumentation Instrumentation should not be an afterthought, but far too often it is. Establishing preferred conditions for a specific drying task requires that you know where you are and where you should be.
Air velocity or flow, temperature, and humidity should be available for each dryer zone. Easily accessible instrument ports are often a great substitute for permanently mounted probes that get fouled or overheated. Input power for each radiant zone should be available on the control panel.
IR pyrometers for measuring web temperatures are great, but they are expensive and easily damaged by overheating and/or fumes in the dryer. An easily accessible port with a removable cover is a good substitute for a permanently mounted pyrometer. Also, make sure the pyrometer isn’t looking at heaters or very hot metal in the dryer.
Pushing a Dryer Too Far
Finally, don’t push a dryer beyond its design limits. The width of the wetted web should not exceed the width that can be heated uniformly.
If web speed or solvent coating weight is too high, we may be tempted to raise temperatures and/or air velocities to accommodate the additional drying load, and that may work. However, it also may cause problems such as skinning, coating disturbances, higher residual moisture, and unforeseen morphological changes in the coating.
Dr. Neil I. Steinberg is chief engineer with Somerset Engineering, Greer, SC, a consulting firm specializing in web processing and related technology. He is a retired DuPont senior research fellow and was DuPont's corporate polyester film technology steward. Steinberg has extensive experience with the manufactur and coating of polyester and similar films. Current technical interests include coating, drying, polymer processing, heat transfer, process control, and mathematical modeling. He can be reached at This email address is being protected from spambots. You need JavaScript enabled to view it..
The views and opinions expressed in Technical Reports are those of the author(s), not those of the editors of PFFC. Please address comments to author(s).